Ich möchte euch mal meinen Bandschleifer vorstellen, der "Stückchenweise" im letzten Jahr entstanden ist.
Nach einer kurzen Phase mit einem masochistischen Chinesischen Schleifbock, der sich die meiste Zeit wegen des schlechten Bandlaufs in eigene Fleisch geschliffen hat, musste was anderes her.
Das ist draus geworden:
Der Rahmen wurde aus 40x40x2.5 Stahlprofilen geschweißt. Bei der Spannung habe ich mich für eine Gasfeder entschieden. Um mit der Alu-Antriebsscheibe genug Reibung zu erhalten, ist sie relativ stark, etwa 210N. Ich hatte anfangs eine sehr Schwache mit 70N und konnte die Leistung der Maschine nicht ausnutzen. Seit dem Tausch ist auch das Laufverhalten und die Stabilität des Bandes weit besser.
Inzwischen ist auch ein Kontaktrad und eine Radieschleifeinrichtung dazugekommen. Die Montage der Aufsätze funktioniert immer nach dem gleichen Prinzip: Vorn eine Hebelschraube als "Drehpunkt", hinten ein Bolzen, der in einem Langloch im jeweiligen Aufsatz sitzt und von einem Griffhebel mit Innengewinde angezogen wird. Das erlaubt bei der Flachschleifeinrichtung die Winkelverstellung, beim Kontaktrad eine Höhenverstellung, um in Kombination mit dem Schleiftisch (Bilder reiche ich bei Interesse nach) genau den Mittelpunkt eines Hohlschliffes (z.B. Rasiermesser) zu justieren.
Der Motor ist ein alter Kreissägenmotor (2-poliger Drehstrommotor) mit 1.5kW, den ich günstig ersteigert habe. Weiters habe ich einen 2.2kW FU, der in einem hübschen Schaltschrank staubfrei untergebracht ist. Mit der 17cm-Antriebsscheibe und einem Frequenzbereich 8-60Hz komme ich auf bis zu ~33m/s.
Für den FU gibt es ein kleines, selbstgebautes Steuergerät. Hier hat ein Poti zur Drehzahlwahl, ein Drehrichtungsschalter und eine LED zur Warnung vor baldiger Überhitzung des FU-Kühlkörpers Platz. Die LED ist auch bei Dauerbetrieb im Hochsommer noch nie angegangen, obwohl dann ab einer gewissen Belastung der FU-Lüfter auf Dauerbetrieb geht.
Maschineparkmäßig hatte ich nur eine Fräse (damals
). Ich drehe zwar viel darauf (Horizontalspindel) aber ich habe bei großen Spanndurchmessern ein Problem, da meine größte Spannzange nur 20mm hat und die Fräse naturgemäß keine Spindelbohrung hat.
Hab ich mir daher die Rollen drehen lassen und dann die Spannrolle auf der Fräse noch ballig überarbeitet. (hier konnte ich dann schon einen Spanndorn fertigen)
Bei der Antriebsrolle habe ich lang überlegt und wollte weder ein Kontaktrad "Verschwenden" noch eine sündteure Flachriemenscheibe oder ähnliches Kaufen. Daher hab ich mich letztlich entschieden, das Ding auf der Fräse+Rundtisch aus dem Vollen zu fertigen.
Da der Rundtisch 3 T-Nuten hat, mussten mal 3 Befestigungslöcher gebohrt werden.
Der Messerkopf hatte seine Freude, die werkstättlichen Reinigungsgeräte auch
Ich bin unter ständigem Kurbeln am Runtisch Schraubenförmig mit etwa 3mm Steigung ins Material eingetaucht. Am Abend hat man dann auch einen kleinen Krampf im Arm
Der Kreissägenmotor passt mir insofern gut, weil der eine Aufnahme für 27mm hat. Die Scheibe hat natürlich die gleiche Bohrung erhalten. Ein bisschen Zittern, ob man nicht in den darunterliegenden Rundtisch fräst, aber das letzte Zehntel Alu bricht eh von selber aus.
27mm ist zufällig auch ein gängiges Maß für Fräser-Spanndorne, und somit gehts auf die Horizontalspindel zum Drehen. Davor wurde noch die hintere Stirnseite plangefräst.
Knapp daneben ist auch ausreichend....
Stufenweise die ballige Fläche vordrehen und mit der Feile und Schleifpapier schlichten.
...So gehts also auch. Besonders dieser Teil des Baus hat mir Spaß gemacht und vor allem sind die Kosten mit 35€ fürs Rundmaterial echt überschaubar. Die Genauigkeit auf dem Motor passt mit 0.02mm auch und die ballige Fläche sorgt für ein feines Laufverhalten.
Ich hoffe euch gefällts und ihr findet vielleicht das eine oder andere interessant. Kritik oder Fragen sind erwünscht!
Schöne Feiertage!
Oliver
Nach einer kurzen Phase mit einem masochistischen Chinesischen Schleifbock, der sich die meiste Zeit wegen des schlechten Bandlaufs in eigene Fleisch geschliffen hat, musste was anderes her.
Das ist draus geworden:
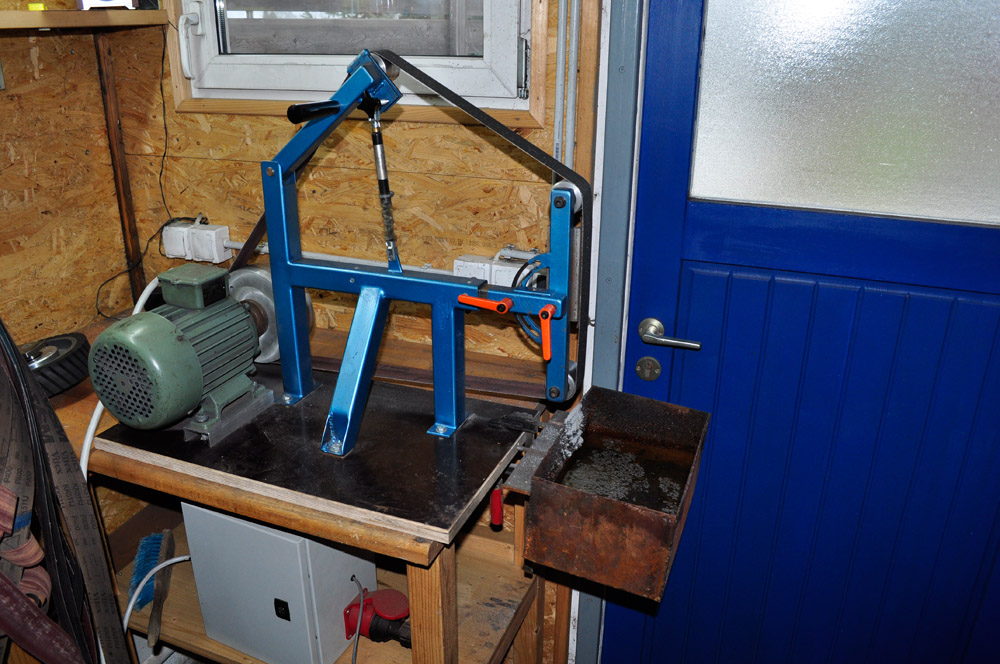
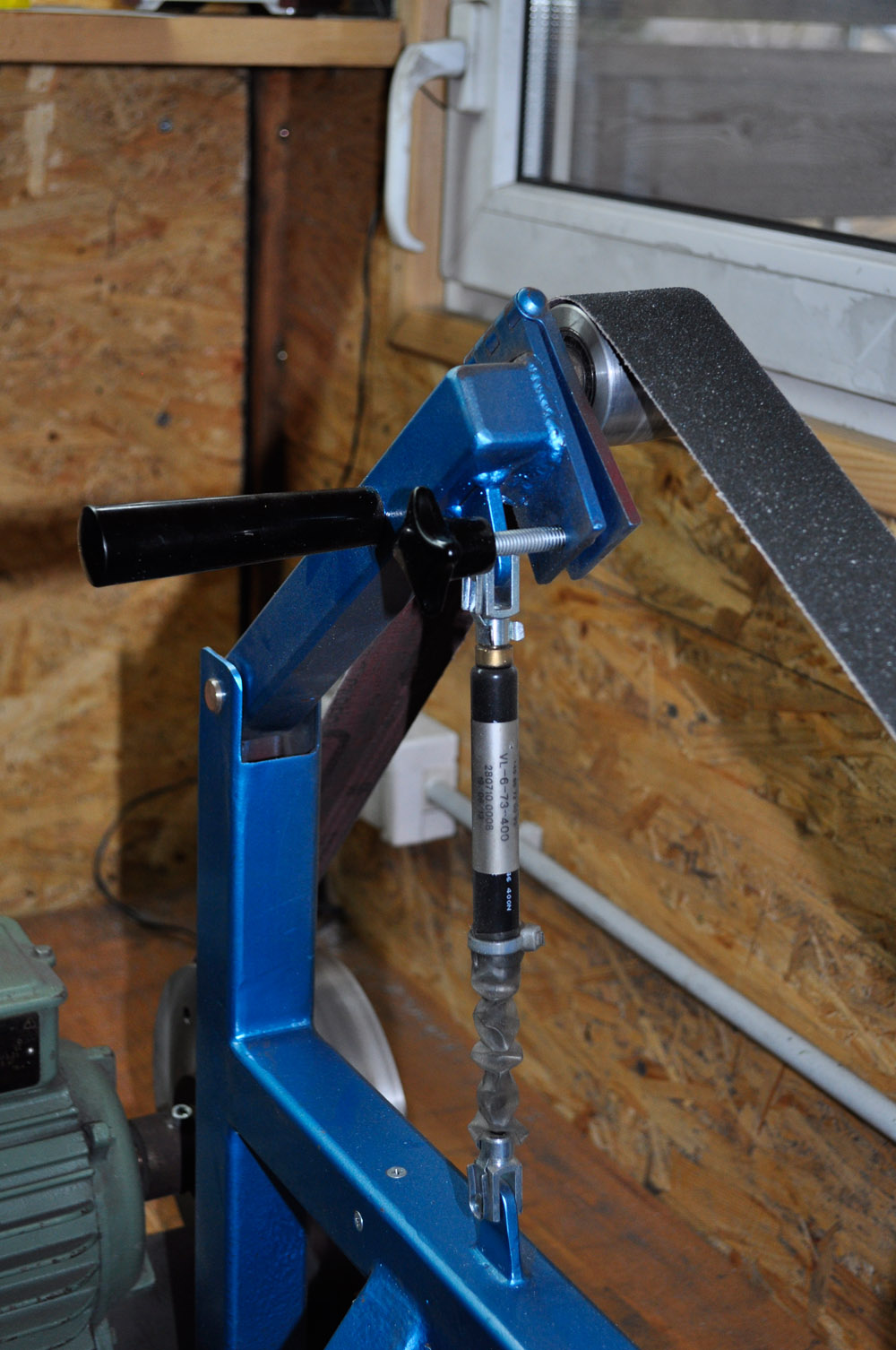
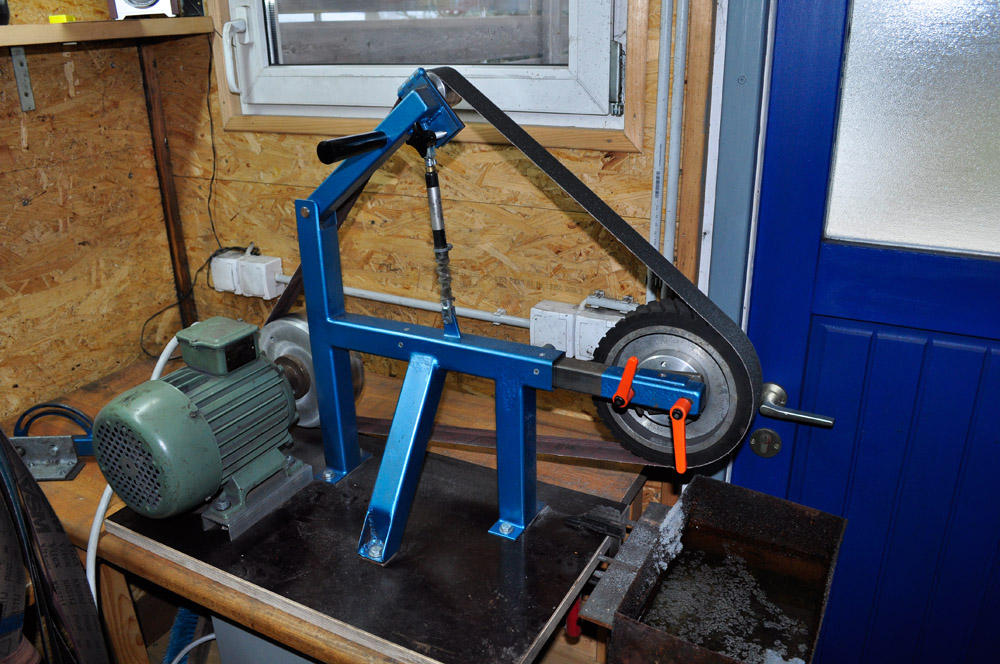
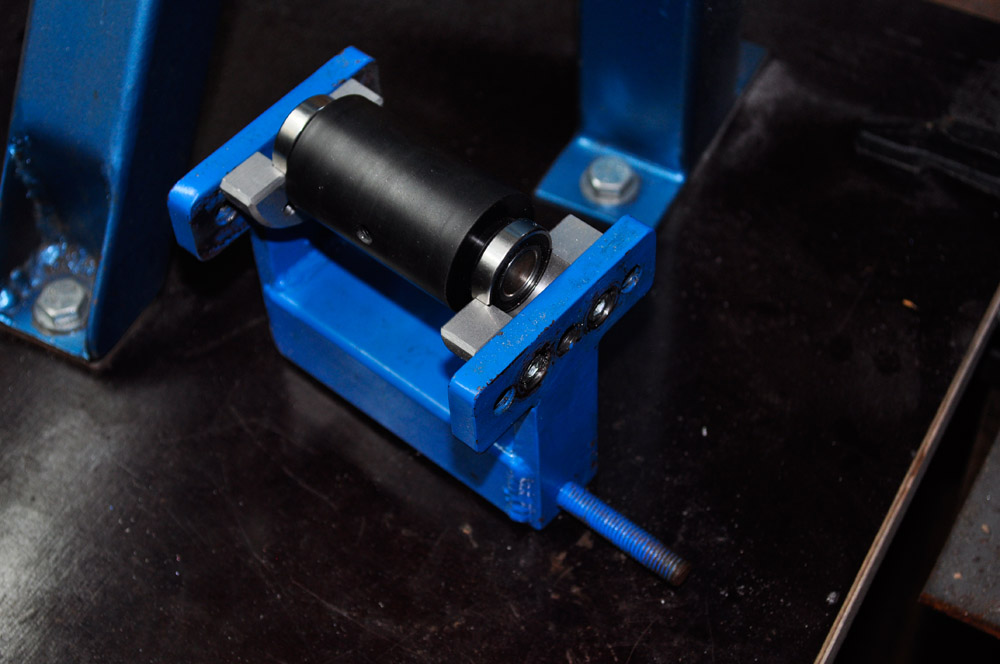
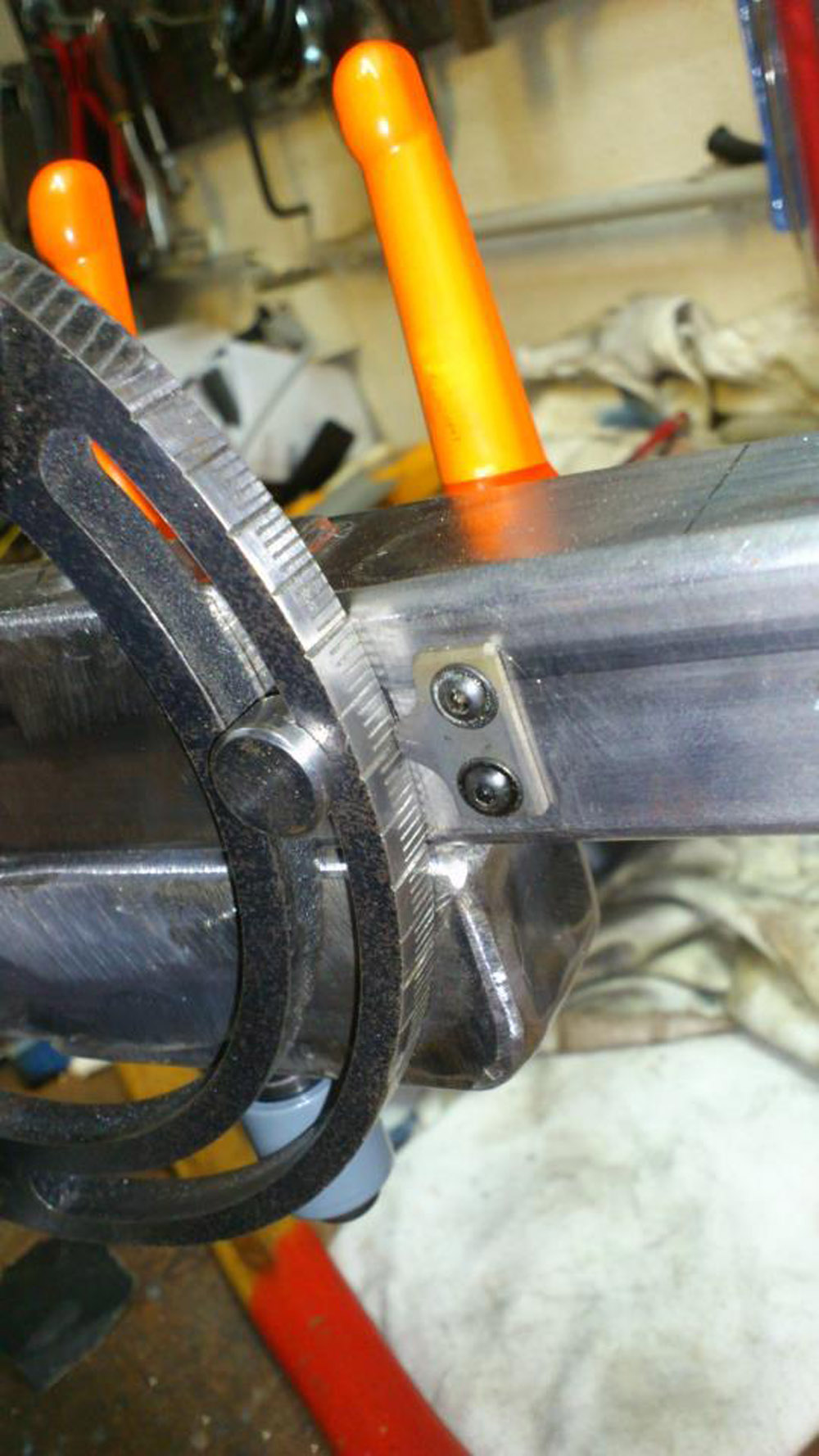
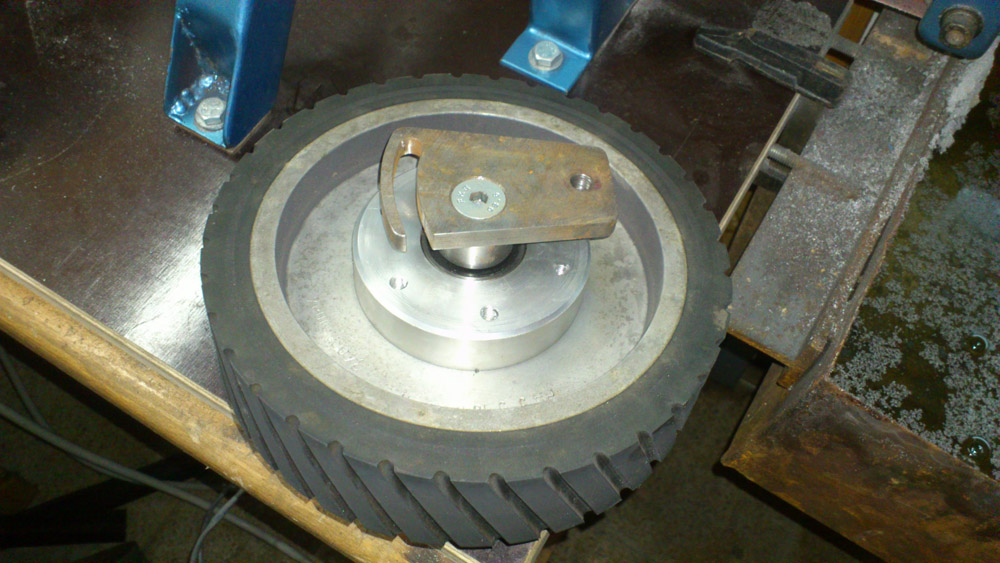
Der Rahmen wurde aus 40x40x2.5 Stahlprofilen geschweißt. Bei der Spannung habe ich mich für eine Gasfeder entschieden. Um mit der Alu-Antriebsscheibe genug Reibung zu erhalten, ist sie relativ stark, etwa 210N. Ich hatte anfangs eine sehr Schwache mit 70N und konnte die Leistung der Maschine nicht ausnutzen. Seit dem Tausch ist auch das Laufverhalten und die Stabilität des Bandes weit besser.
Inzwischen ist auch ein Kontaktrad und eine Radieschleifeinrichtung dazugekommen. Die Montage der Aufsätze funktioniert immer nach dem gleichen Prinzip: Vorn eine Hebelschraube als "Drehpunkt", hinten ein Bolzen, der in einem Langloch im jeweiligen Aufsatz sitzt und von einem Griffhebel mit Innengewinde angezogen wird. Das erlaubt bei der Flachschleifeinrichtung die Winkelverstellung, beim Kontaktrad eine Höhenverstellung, um in Kombination mit dem Schleiftisch (Bilder reiche ich bei Interesse nach) genau den Mittelpunkt eines Hohlschliffes (z.B. Rasiermesser) zu justieren.
Der Motor ist ein alter Kreissägenmotor (2-poliger Drehstrommotor) mit 1.5kW, den ich günstig ersteigert habe. Weiters habe ich einen 2.2kW FU, der in einem hübschen Schaltschrank staubfrei untergebracht ist. Mit der 17cm-Antriebsscheibe und einem Frequenzbereich 8-60Hz komme ich auf bis zu ~33m/s.
Für den FU gibt es ein kleines, selbstgebautes Steuergerät. Hier hat ein Poti zur Drehzahlwahl, ein Drehrichtungsschalter und eine LED zur Warnung vor baldiger Überhitzung des FU-Kühlkörpers Platz. Die LED ist auch bei Dauerbetrieb im Hochsommer noch nie angegangen, obwohl dann ab einer gewissen Belastung der FU-Lüfter auf Dauerbetrieb geht.
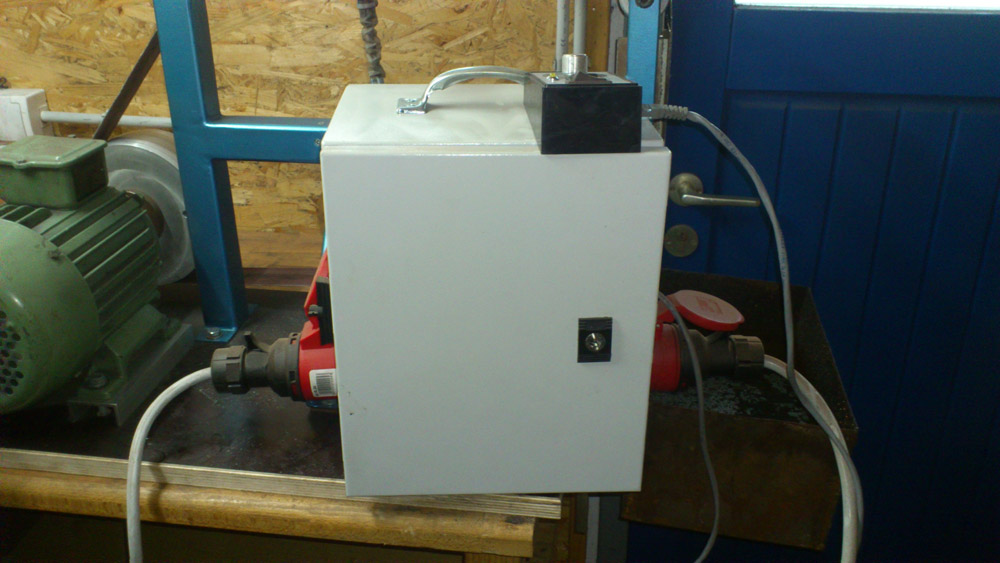
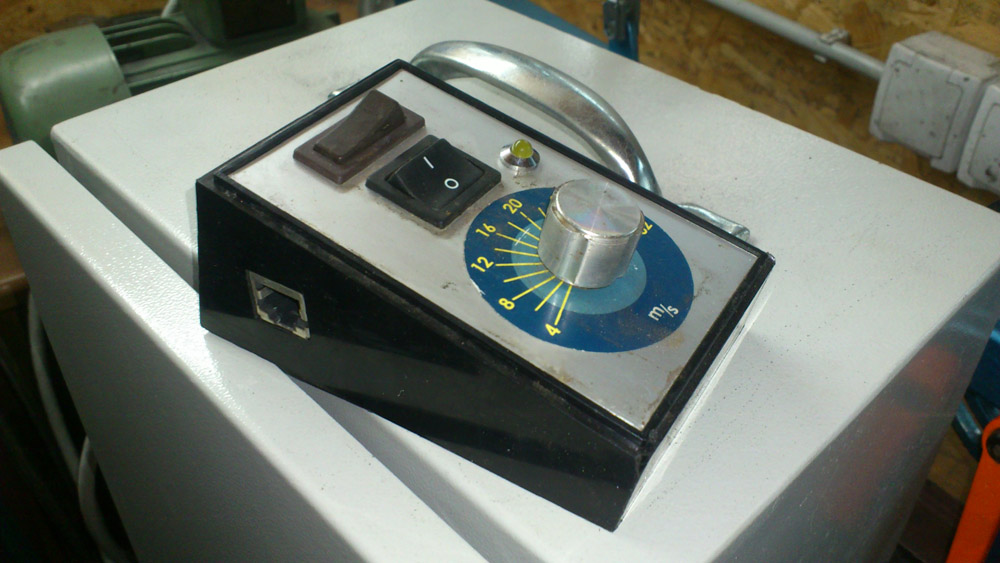
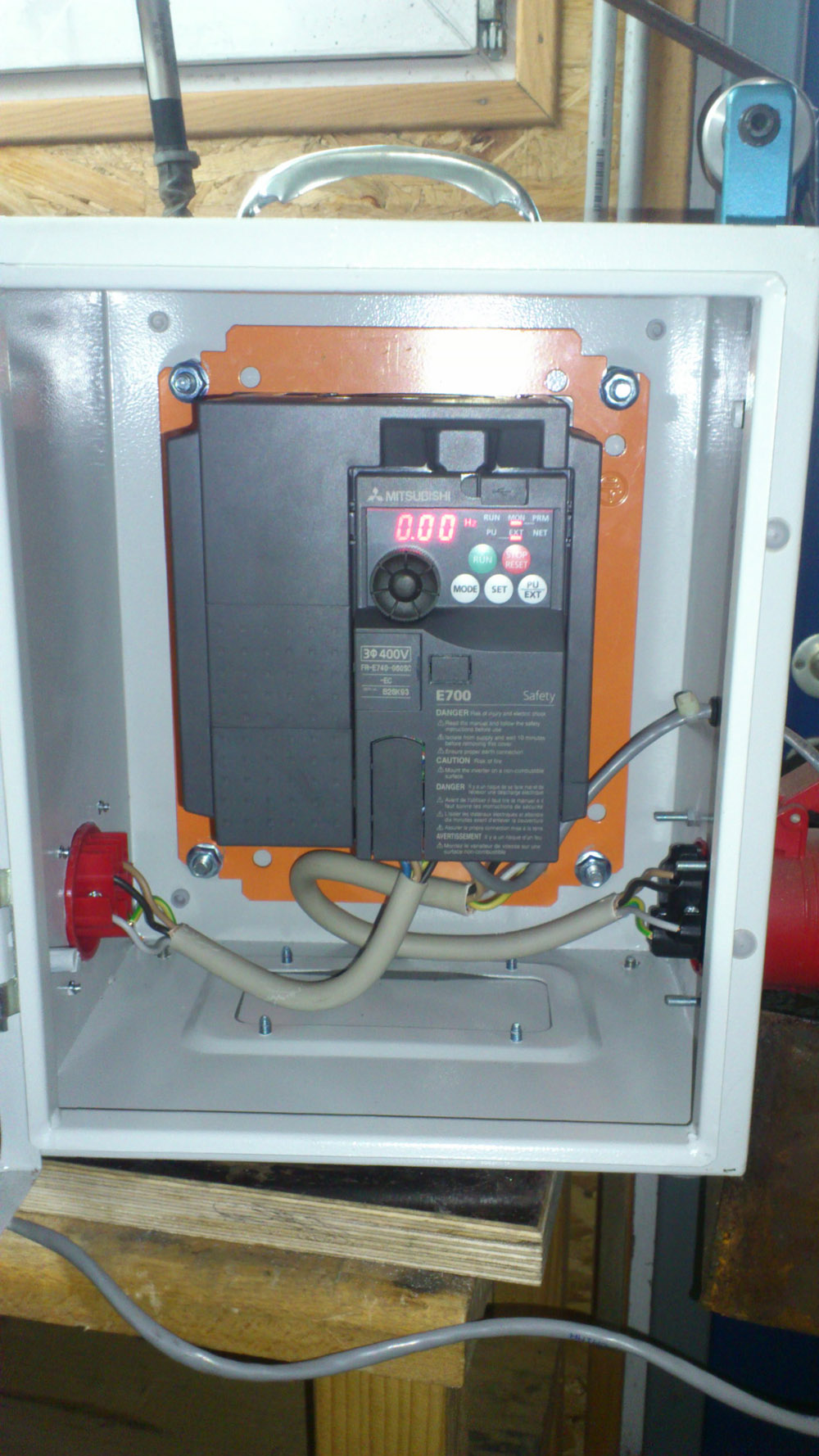
Maschineparkmäßig hatte ich nur eine Fräse (damals

Hab ich mir daher die Rollen drehen lassen und dann die Spannrolle auf der Fräse noch ballig überarbeitet. (hier konnte ich dann schon einen Spanndorn fertigen)
Bei der Antriebsrolle habe ich lang überlegt und wollte weder ein Kontaktrad "Verschwenden" noch eine sündteure Flachriemenscheibe oder ähnliches Kaufen. Daher hab ich mich letztlich entschieden, das Ding auf der Fräse+Rundtisch aus dem Vollen zu fertigen.
Da der Rundtisch 3 T-Nuten hat, mussten mal 3 Befestigungslöcher gebohrt werden.
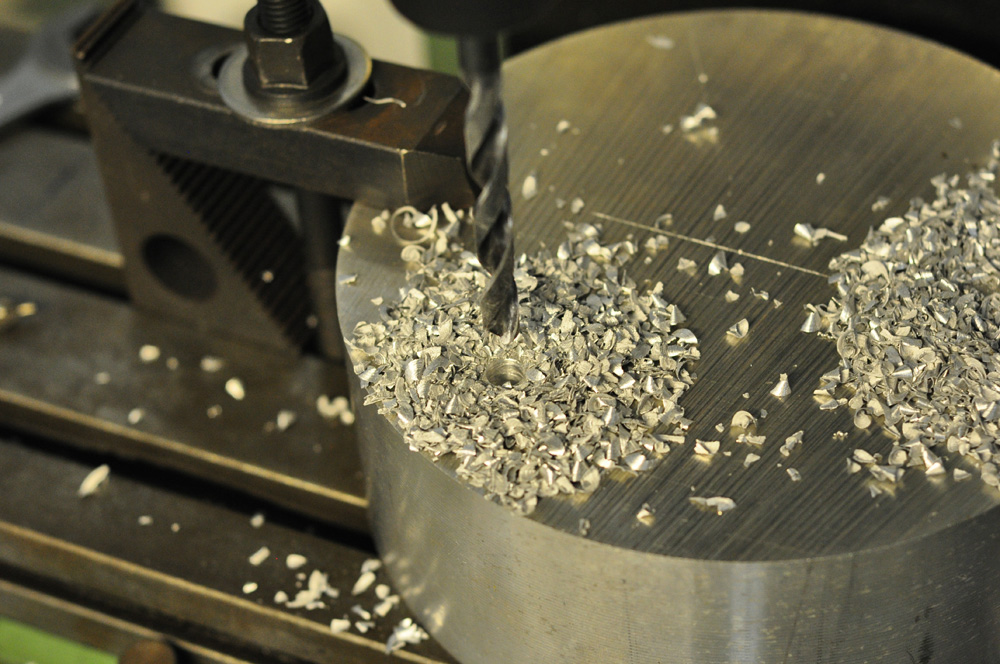
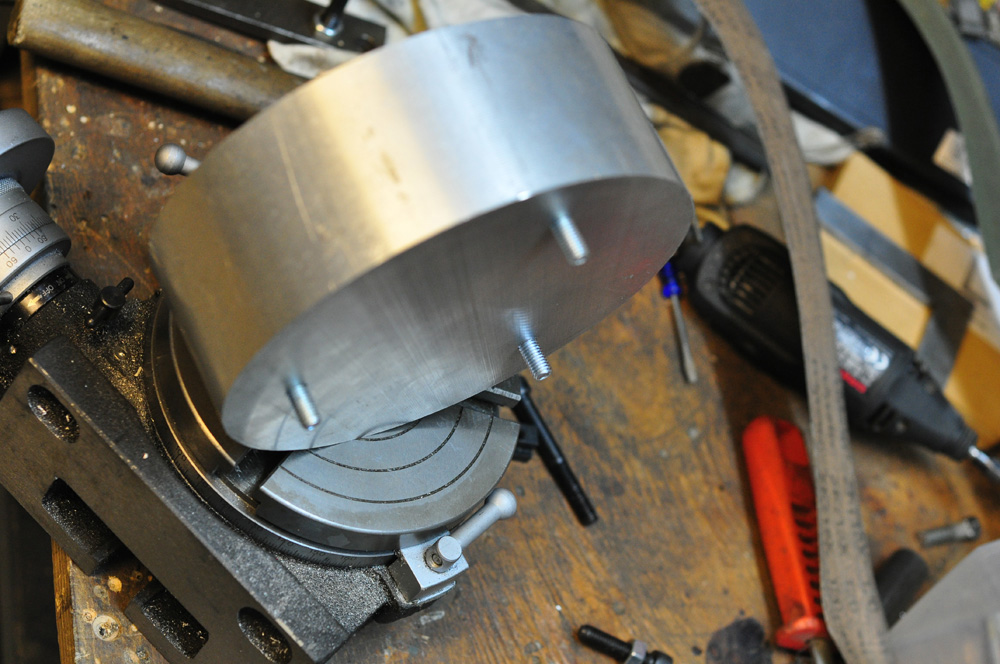
Der Messerkopf hatte seine Freude, die werkstättlichen Reinigungsgeräte auch

Ich bin unter ständigem Kurbeln am Runtisch Schraubenförmig mit etwa 3mm Steigung ins Material eingetaucht. Am Abend hat man dann auch einen kleinen Krampf im Arm
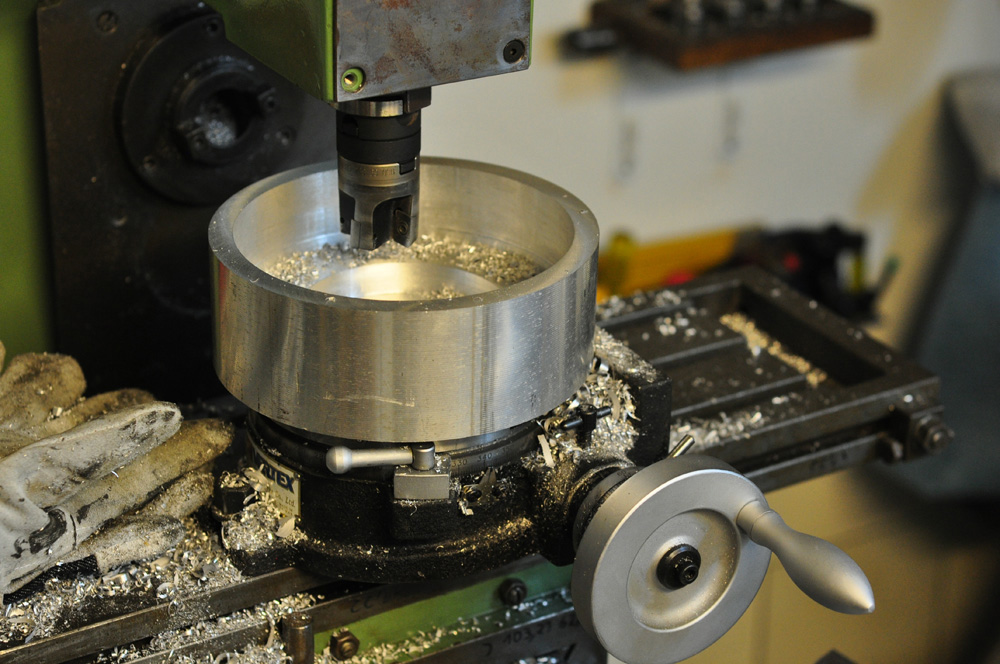
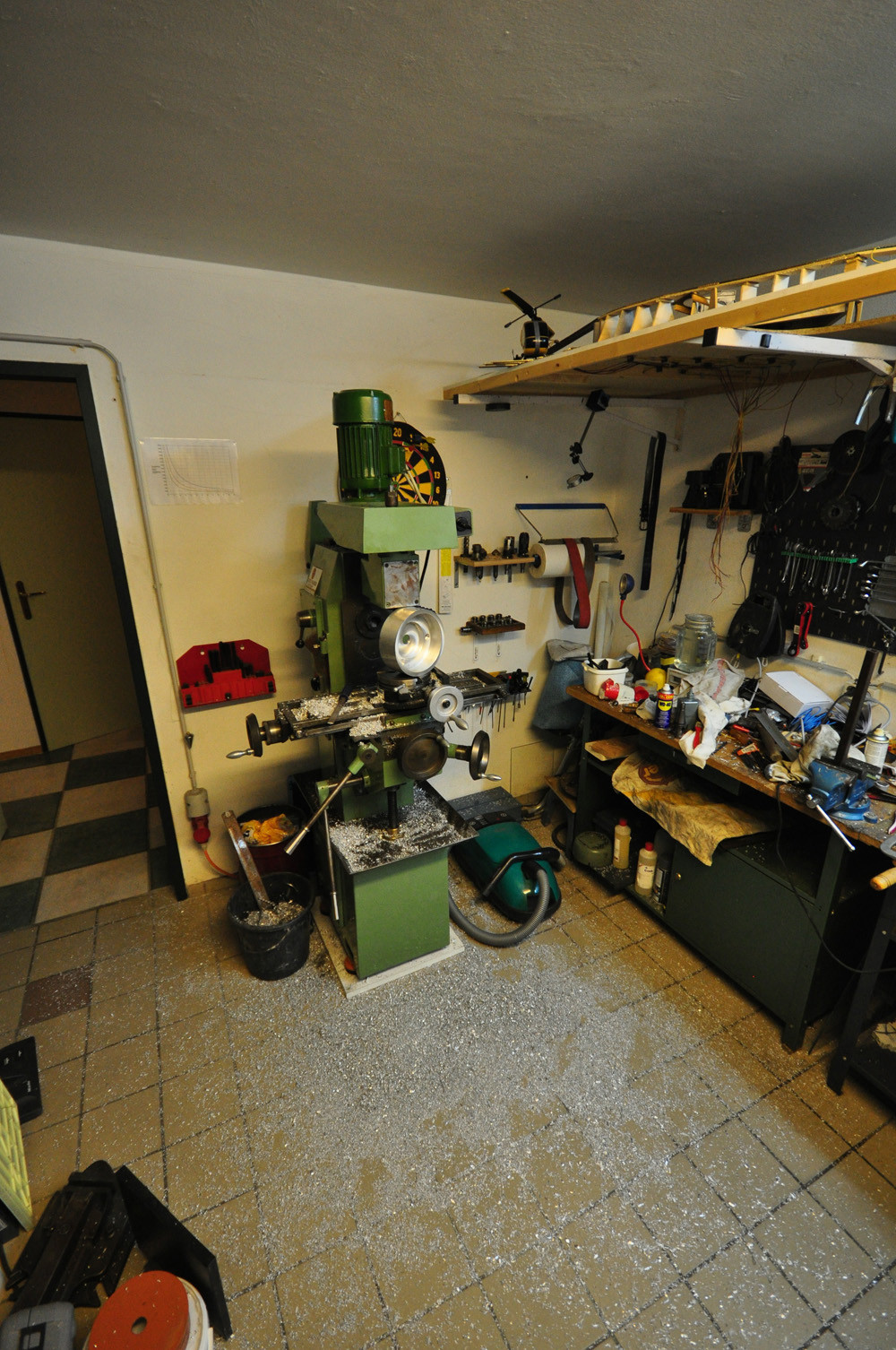
Der Kreissägenmotor passt mir insofern gut, weil der eine Aufnahme für 27mm hat. Die Scheibe hat natürlich die gleiche Bohrung erhalten. Ein bisschen Zittern, ob man nicht in den darunterliegenden Rundtisch fräst, aber das letzte Zehntel Alu bricht eh von selber aus.
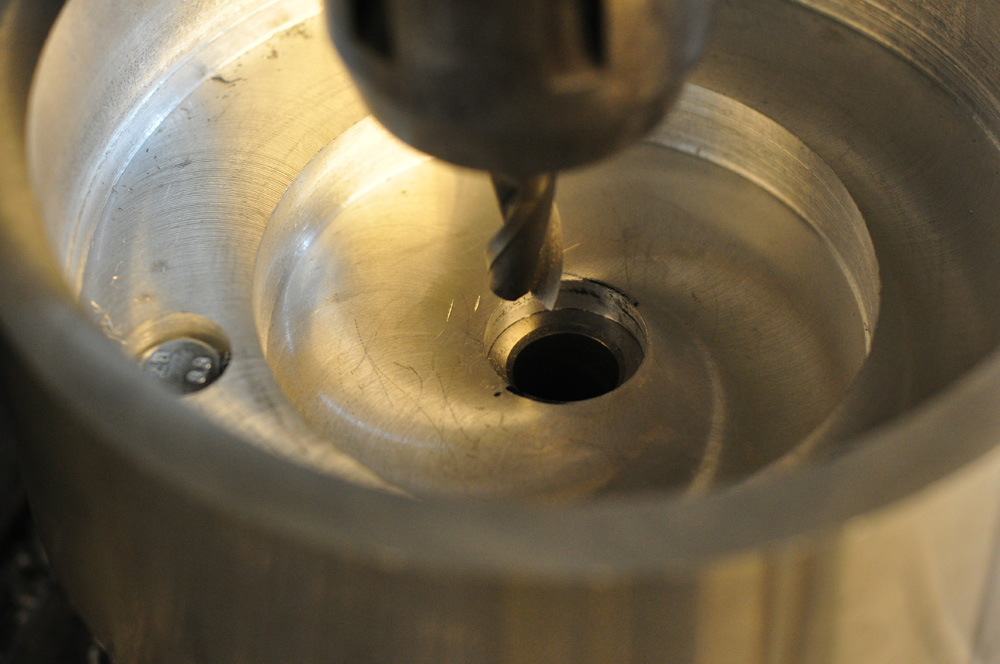
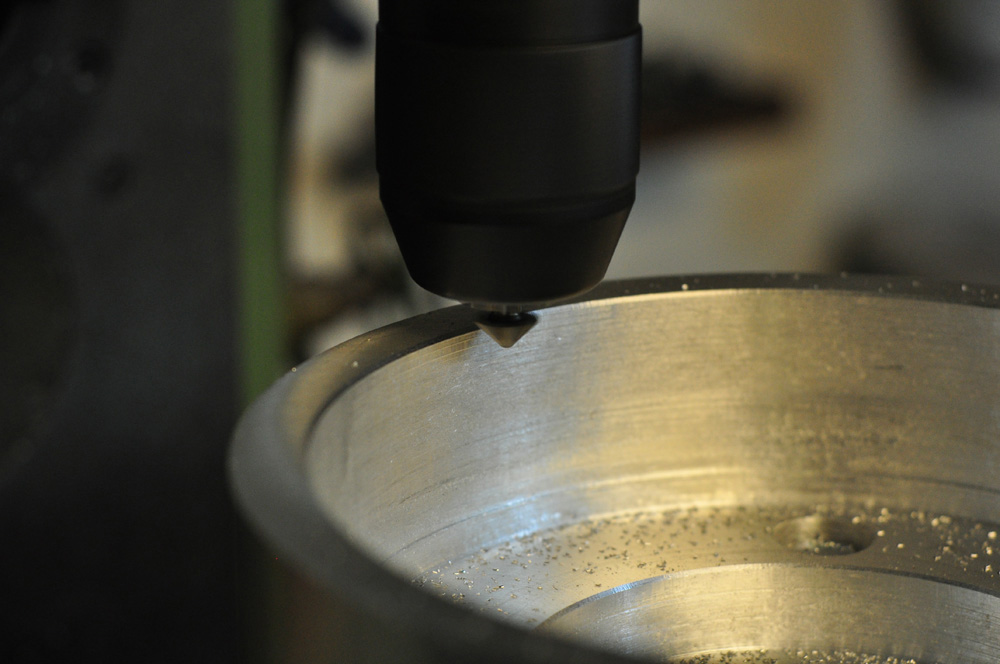
27mm ist zufällig auch ein gängiges Maß für Fräser-Spanndorne, und somit gehts auf die Horizontalspindel zum Drehen. Davor wurde noch die hintere Stirnseite plangefräst.
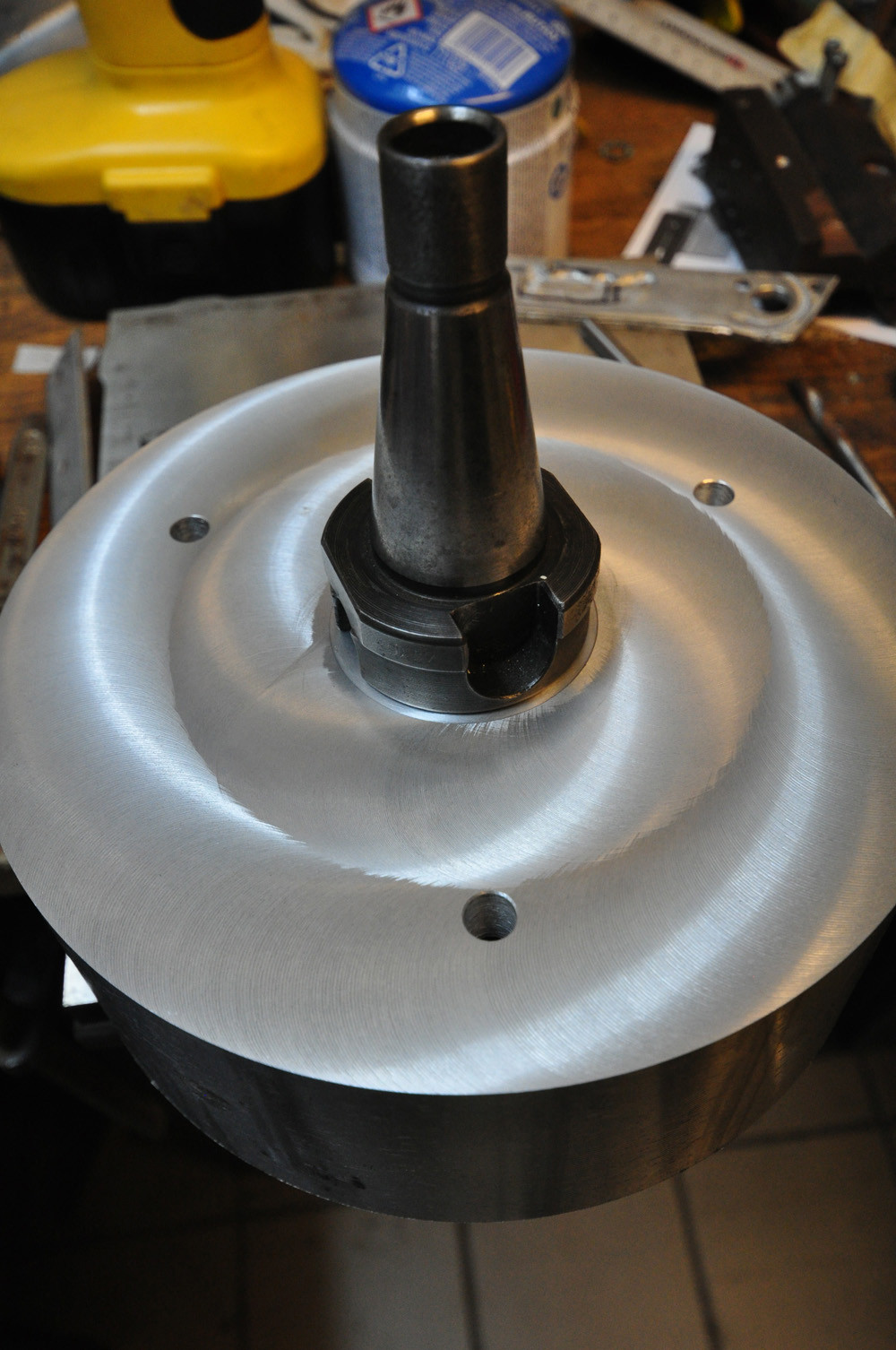
Knapp daneben ist auch ausreichend....
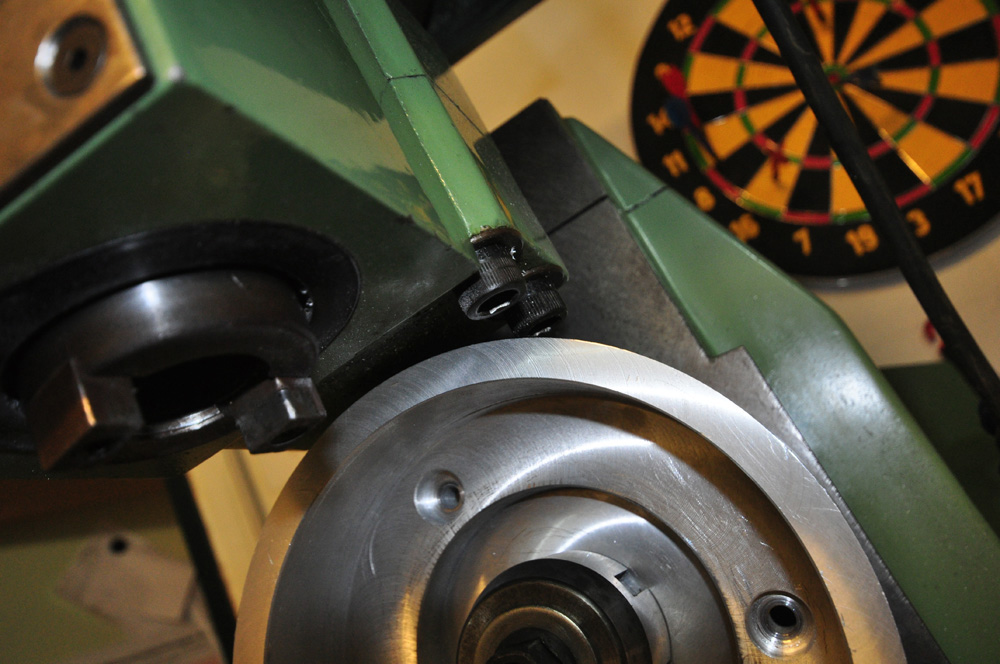

Stufenweise die ballige Fläche vordrehen und mit der Feile und Schleifpapier schlichten.
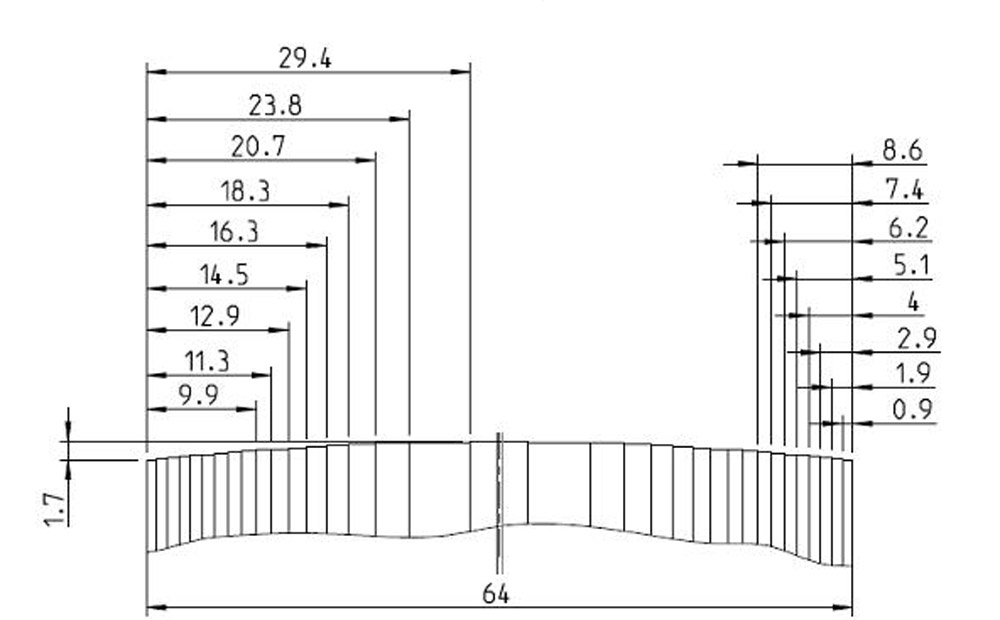
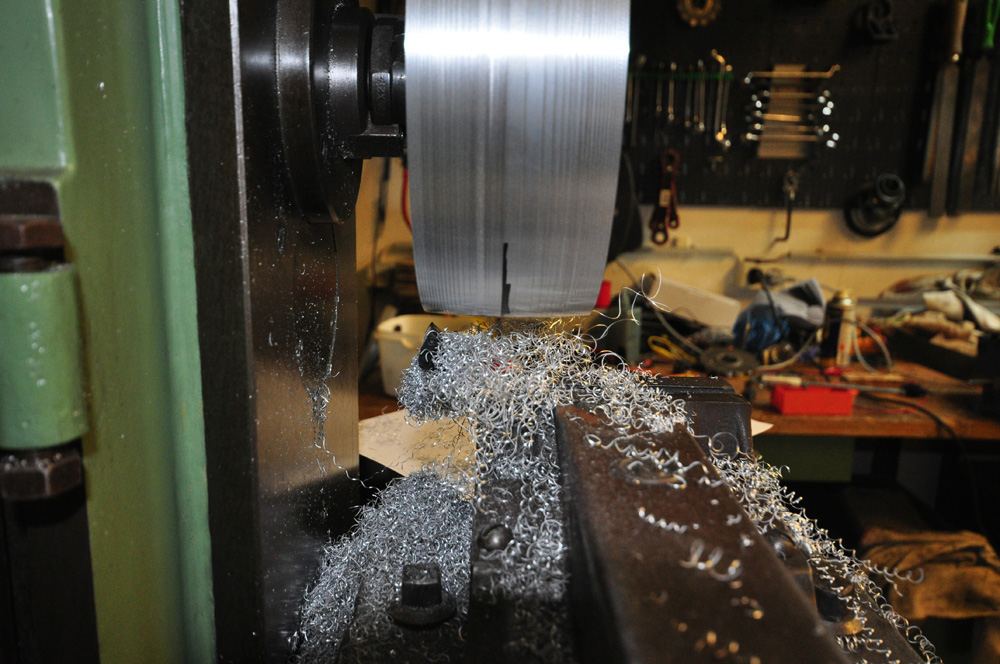
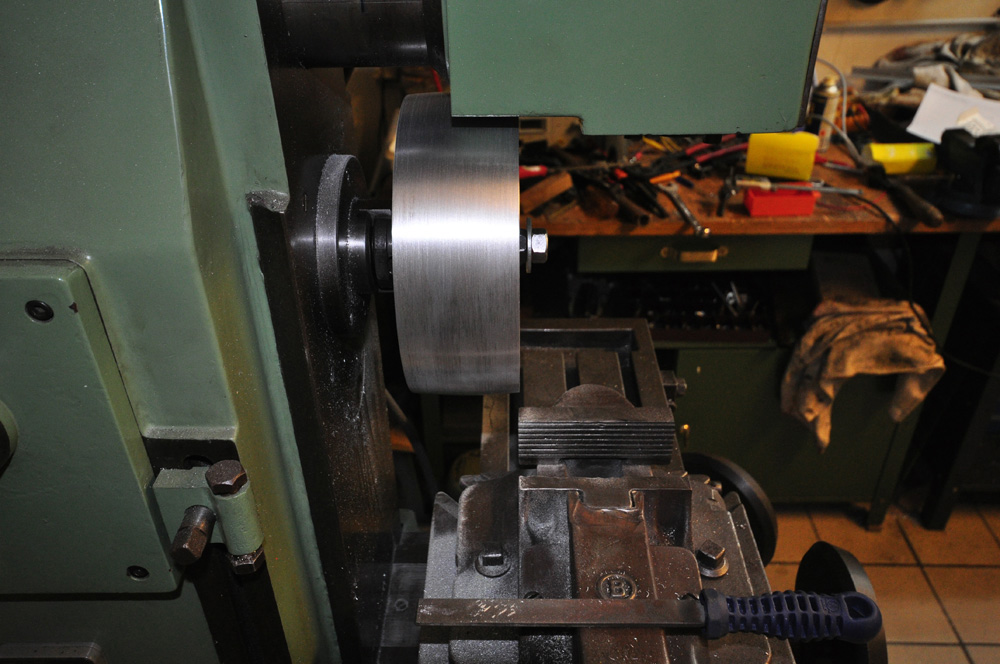
...So gehts also auch. Besonders dieser Teil des Baus hat mir Spaß gemacht und vor allem sind die Kosten mit 35€ fürs Rundmaterial echt überschaubar. Die Genauigkeit auf dem Motor passt mit 0.02mm auch und die ballige Fläche sorgt für ein feines Laufverhalten.
Ich hoffe euch gefällts und ihr findet vielleicht das eine oder andere interessant. Kritik oder Fragen sind erwünscht!
Schöne Feiertage!
Oliver
Zuletzt bearbeitet: