Currently busy with modifying another large sawback scout knife, this one manufactured by the no longer existing Solingen based firm of Kronenkrebs.
The stag handle was way too thick for my hands, and the low sabergrind geometry was far from ideal for it's intended use as a large allround camp knife / chopper.
The quality of the drop-forged steel in the blade however makes it worthwile for me to put in some elbow grease.
This is how the knife looked when i bought it:
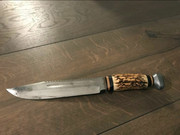
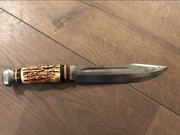
First i ground the old "edge" flat on the Tormek SB-250 stone, then ground down the blade's center ridges on both sides with a Chinese 120 grit diamond file, then reshaped the blade from a low sabergrind into a full convex one with the help of a somewhat modified cheap Parkside linisher that can now also be used as a slack belt grinder.
This is the machine i have:
https://www.youtube.com/watch?v=sHvbVhnNuAU
Refining the blade surfaces as well as the actual forming & refining of the apex area was done by hand on grits 240 and 400 wet & dry paper using WD40 as a lubricant, while the burr was removed on the Tormek leather wheel.
The new apex can whittle a chest hair from hair root to hair tip @ about 30 degrees inclusive.
The grinding & sanding of the blade also automatically resharpened the sawback's teeth, and the full convex blade shape makes that the sawback is now the blade's thickest part, which reduces the chances of jamming when using it for sawing or notching.
The slack belt linisher also proved very useful for shaping a new handle made from 12 thick rubber washers, each one cut from an old piece of very wear resistant & triple fiber weave reinforced industrial conveyor belt.
The ground & shaped rubber has a very nice tactile feel to it and i suspect that it will also dampen shock quite effectively, which will aid it's use in it's intended role.
Also made a thick aluminium guard as a replacement for the factory installed useless piece of flimsy brass.
Guard & pommel are now permanently installed using 2-ton epoxy, while each rubber washer is glued to the next with a good rubber glue which stays flexible.
The knife is now ready for some field testing, and if that turns out satisfactory some more refining steps will follow.
This is how it currently looks (sheath has been waxed but still needs to be restitched):

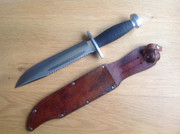
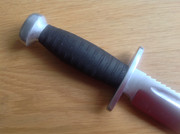
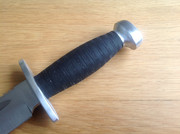
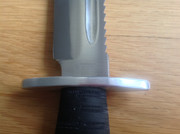
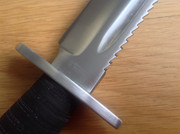

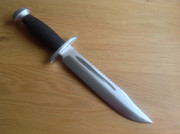
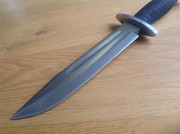
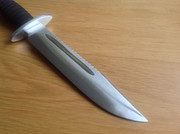
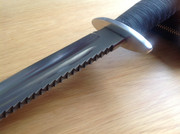
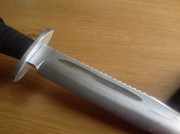
Specs:
Overall length: 33,5 cm (13.9 inch)
Blade length: 21,0 cm (8.27 inch)
Max blade thickness: 5,7 mm
Steel type: drop-forged low alloy carbon steel
Handle materials: Aluminium guard & pommel with rubber washers
Weight: 388 grams
Sheath: leather
The stag handle was way too thick for my hands, and the low sabergrind geometry was far from ideal for it's intended use as a large allround camp knife / chopper.
The quality of the drop-forged steel in the blade however makes it worthwile for me to put in some elbow grease.
This is how the knife looked when i bought it:
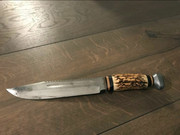
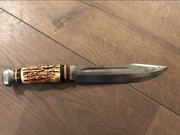
First i ground the old "edge" flat on the Tormek SB-250 stone, then ground down the blade's center ridges on both sides with a Chinese 120 grit diamond file, then reshaped the blade from a low sabergrind into a full convex one with the help of a somewhat modified cheap Parkside linisher that can now also be used as a slack belt grinder.
This is the machine i have:
https://www.youtube.com/watch?v=sHvbVhnNuAU
Refining the blade surfaces as well as the actual forming & refining of the apex area was done by hand on grits 240 and 400 wet & dry paper using WD40 as a lubricant, while the burr was removed on the Tormek leather wheel.
The new apex can whittle a chest hair from hair root to hair tip @ about 30 degrees inclusive.
The grinding & sanding of the blade also automatically resharpened the sawback's teeth, and the full convex blade shape makes that the sawback is now the blade's thickest part, which reduces the chances of jamming when using it for sawing or notching.
The slack belt linisher also proved very useful for shaping a new handle made from 12 thick rubber washers, each one cut from an old piece of very wear resistant & triple fiber weave reinforced industrial conveyor belt.
The ground & shaped rubber has a very nice tactile feel to it and i suspect that it will also dampen shock quite effectively, which will aid it's use in it's intended role.
Also made a thick aluminium guard as a replacement for the factory installed useless piece of flimsy brass.
Guard & pommel are now permanently installed using 2-ton epoxy, while each rubber washer is glued to the next with a good rubber glue which stays flexible.
The knife is now ready for some field testing, and if that turns out satisfactory some more refining steps will follow.
This is how it currently looks (sheath has been waxed but still needs to be restitched):

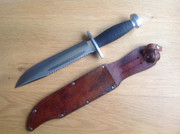
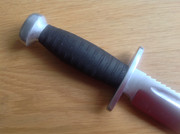
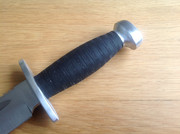
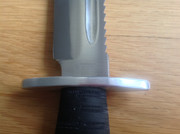
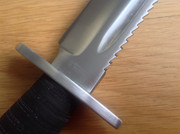

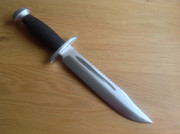
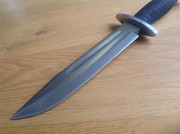
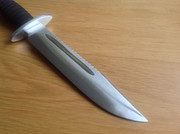
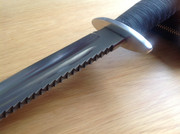
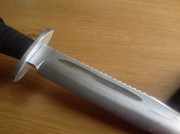
Specs:
Overall length: 33,5 cm (13.9 inch)
Blade length: 21,0 cm (8.27 inch)
Max blade thickness: 5,7 mm
Steel type: drop-forged low alloy carbon steel
Handle materials: Aluminium guard & pommel with rubber washers
Weight: 388 grams
Sheath: leather